Every day there seems to be yet another article about how robots and the rise of artificial intelligence will take over our daily work in a whole host of industries from transport to construction, call centres to finance and law to journalism and other service industries.
In truth it's manufacturing and logistics where the rise of robotics is really being felt at the moment. One set of estimates online suggests that up to 20 million manufacturing jobs around the world could be replaced by robots by 2030 with each new industrial robot replacing 1.6 traditional manufacturing jobs. It cites that the number of robots in use worldwide has multiplied three-fold over the past two decades, to around 2.25 million.
Based on their assessment the more repetitive the job, the greater the risk of its being wiped out. This makes sense to me as logistics and manufacturing is already about productivity and removing waste from the end to end process. Robotics has always been seen as a natural extension of that.
Warehouse automation
Warehouses are key nodes in many supply chains and typically represent over 20% of logistics costs. Major motivations for warehouse automation are typically to reduce material handling; increase accuracy levels; improve service consistency and increase speed of service with a desire to reduce labour cost; increase output rate and improve service availability.
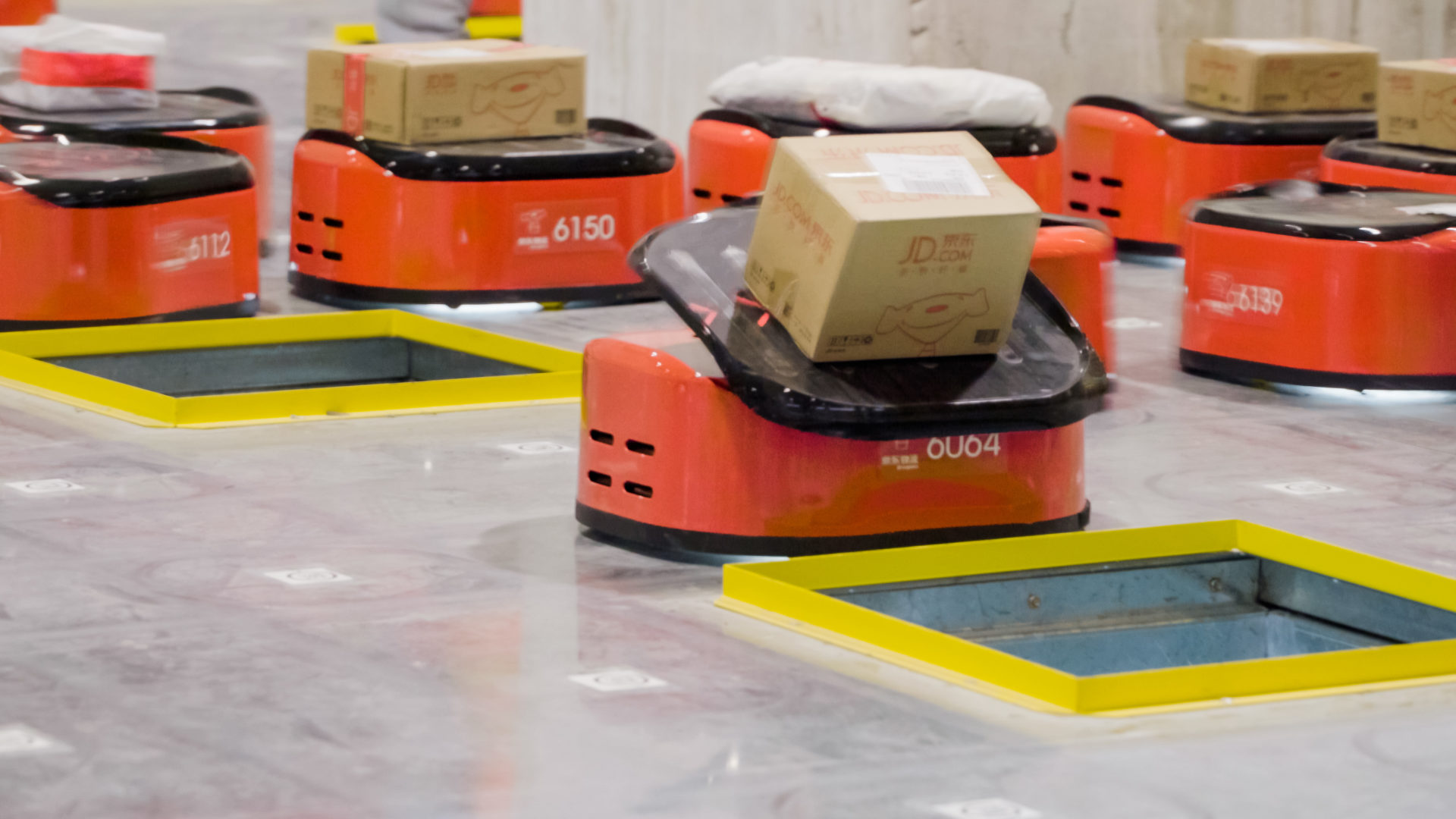
It is important to note that automation projects are normally very complex, involving a number of different systems that need to be designed and developed in parallel, including the equipment itself, the software and the building in which it will be housed. As a result it tends to be of benefit to scale outsource or third party logistics providers, or significant consumer-focused operations, but as with most technologies the price point will come down over time as the technology matures and the supply chain evolves.
It is estimated that in Western Europe, only about 30% of warehouses that would be viable for automation are automated. Total logistics costs vary roughly between 10% and 50% of revenue in different industries so as a result of further efficiency savings potential and the need for more flexible warehouses, more sophisticated automated solutions are starting to be implemented. Automated loading and unloading systems are already available and used by organisations such as Audi, Skoda, P&G, Coca Cola, Indesit, Volvo and in the future these are likely to be able to bypass obstacles and adjust routes automatically (using machine learning).
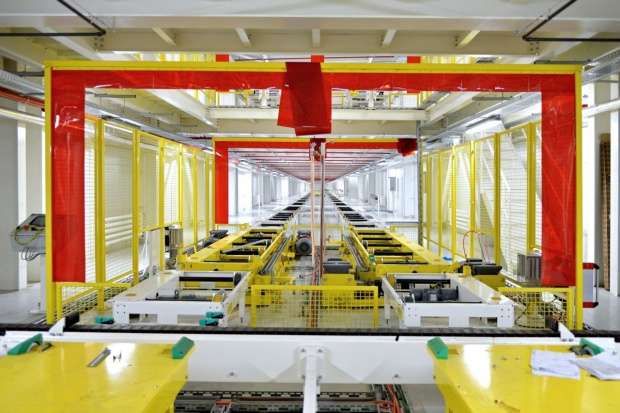
Collaborative robotics
Boston Dynamics’ Altas robot uses 3D printed hardware combined with stereo vision, range sensing and ability to lift up to 11kg. It is envisaged as a cobot, or “collaborative robot”, specially designed to ease human-machine interface and enhance security. Cobots could work with human workers in warehouses and manage risks thanks to their greater sensitivity. Machine learning applications will also allow warehouse operatives to “show” particular functions to a cobot for it to repeat it rapidly and repeatedly.
Trailer and container unloading robots will assist workers in the future warehouse with physically strenuous tasks. Robotic arms equipped with powerful sensors and grippers can already locate items, analyse their size and shape and determine optimal unloading. Assistance robots could be used for local delivery, following delivery staff to transport heavy items, pre- sort parcels inside vehicles and autonomously deliver parcels to dedicated collection points at asset locations or depots.
Autonomous vehicles in warehousing
Autonomous vehicles have a significant future potential – clearly in consumer driving, but increasingly in supply chain, logistics and warehouse operations. Autonomous warehouse technology is being used already to automate picking and packing and load trucks and in future may be used for parcel delivery and last mile delivery. Whilst a number of these technologies are still in pilot adoption, anticipated growth is substantial - by 2035, more than 12 million fully autonomous vehicles are expected to be sold per year globally at a market value of up to $77 billion.
Amazon purchased Kiva for $775 million in 2012 and has developed significant automation of picking and packing in its warehouse operations ever since leading to an estimated 20% p.a. operating cost saving ($22 million in cost savings for each fulfillment centre deployed). Google filed similar patents in 2016 for its own autonomous warehouse technology. In the UK Ocado has evolved from an automated grocery logistics company to a full-scale £1.6bn turnover technology company.
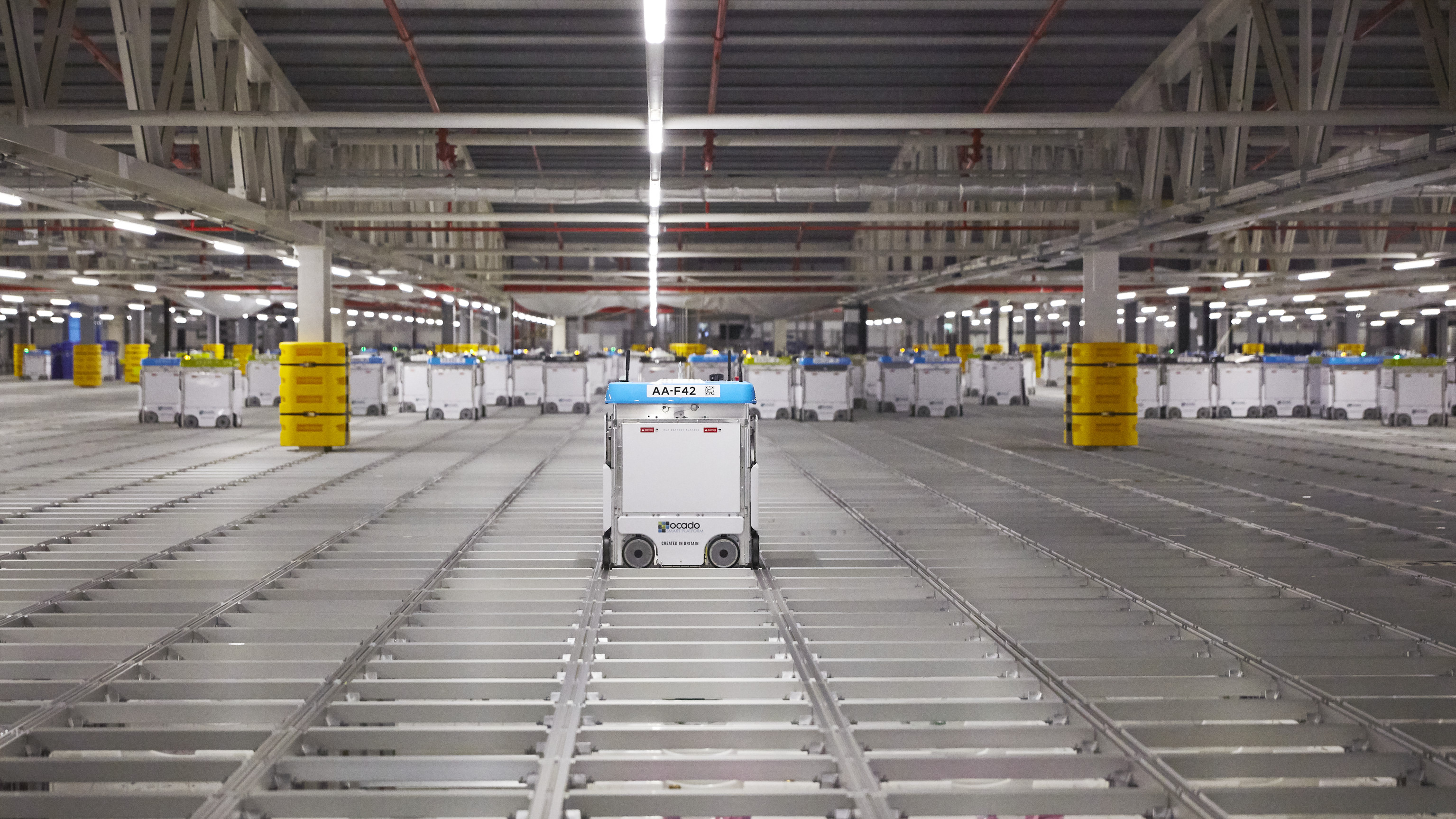
Self-driving vehicles can be used for loading and unloading, warehouse transportation and volume scanning. Examples include KARIS PRO (autonomous vehicles); Open Shuttle, Locus Robotics, Swisslog CarryPick (mobile rack delivery), Fetch Robotics Freight. This growing adoption of goods-to-person automation drives warehouse flexibility and whilst not yet deployable is a trend to watch.
Robotic delivery
Electrical multicopters (vertical take-off and landing) appear most promising for logistics. A range of companies are now developing the first commercial UAVs for delivery including Flirtey (seen as adrone delivery leader) and of course Amazon which made its first UAV delivery in December 2016 in Cambridge and traditional logistics firms such as UPS and DHL. Trials also include the pairing of UAVs with delivery vehicles and remote parcel handover.
Carriers, shippers and logistics providers are looking for an increasing amount of information related to shipments - demanding transparency and automating the flow of information across the supply chain. Fleet telematics is becoming even more embedded with load, trailer and smartphone tracking technology demonstrating productivity benefits and transport efficiency. Vehicles themselves increasingly use remote diagnostic reporting systems that can transmit fault codes to alert carriers to required maintenance.
In April 2016, a convoy of self-driving trucks completed a cross-border trip in Europe (from six major manufacturers— DAF, Daimler, Iveco, MAN, Scania and Volvo) and the likes of Tesla, Volvo, Peterbilt, and Daimler are also focusing on self-driving commercial vehicles.
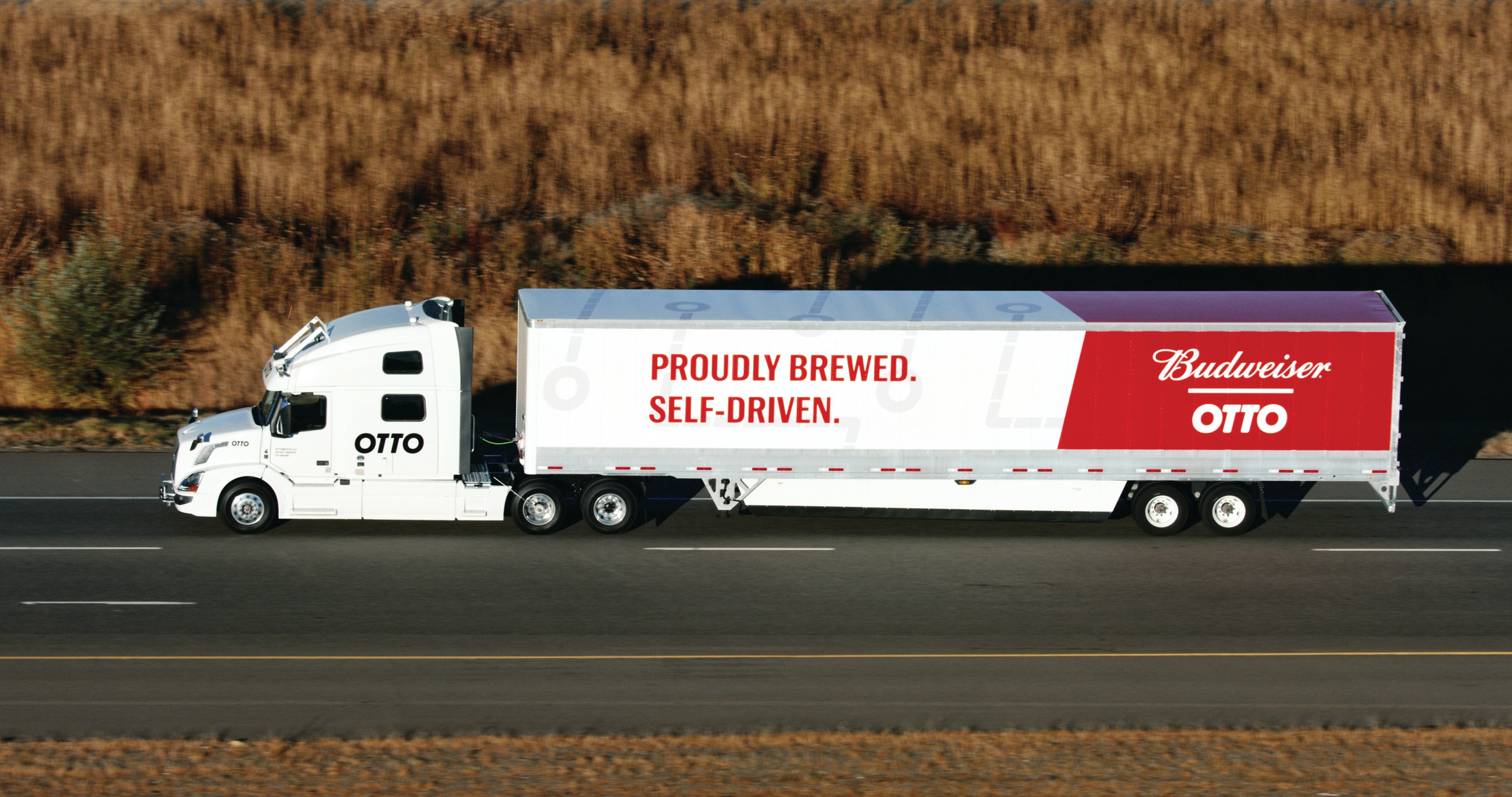
The robot future
Something like every third robot worldwide is installed in China accounting for around 20% of robots worldwide. Cost efficiency, capability and the rise in demand for manufactured goods is driving the ongoing adoption of robots. It is interesting to note that even in industries such as automotive where robotic production lines have been in place for some time the requirements of future autonomous and electric vehicles are requiring new investment in ever more intelligent robots to build them.
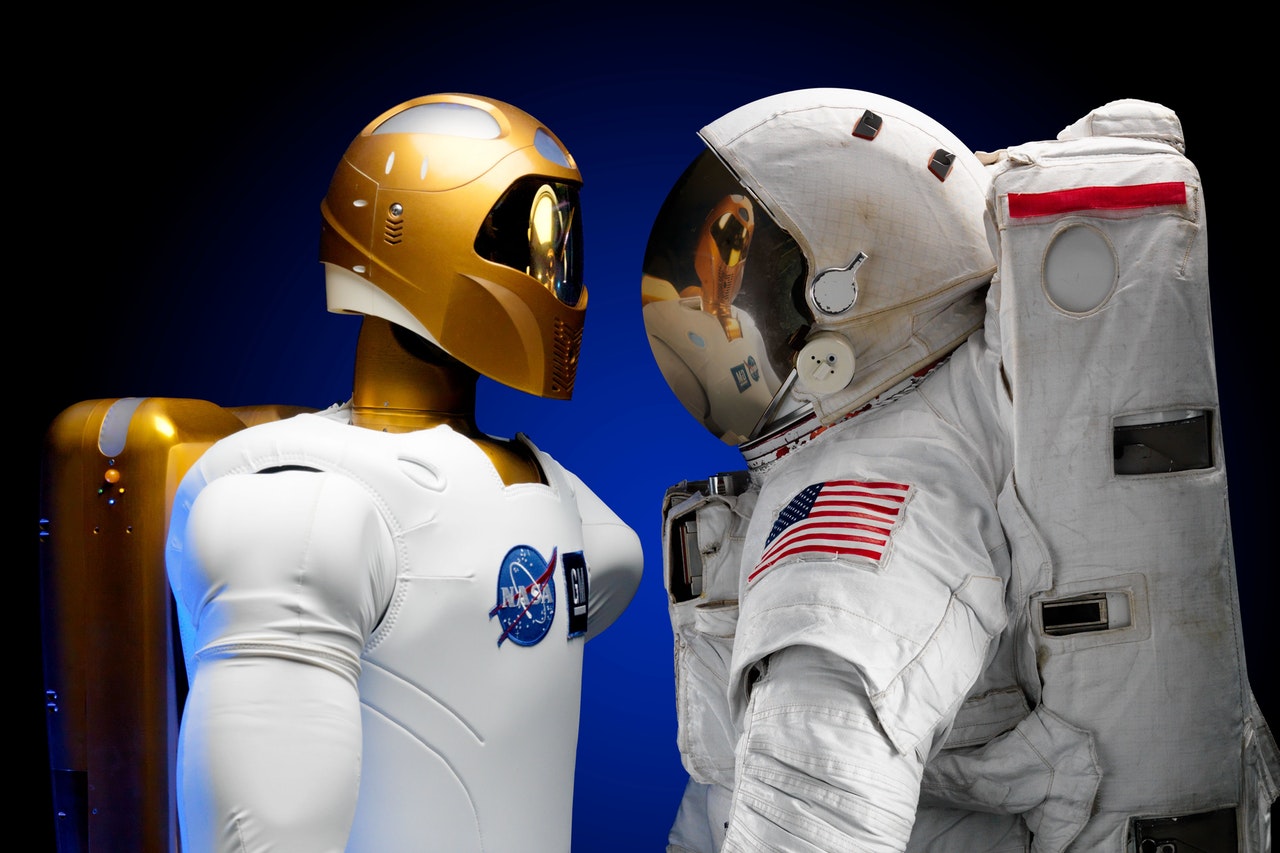
Even more traditional industies such as food manufacturing, packaging and plastics are seeing an increase in robot adoption. There will clearly always be a need for humans to programme, supervise, collaborate with or innovate in the warehouse and logistics environment but in a world where it becomes cheaper to use a robot than a human employee you can see why quite so many articles are being written about the risk of replacing low skilled jobs.
What next?
We can help you to make improvements in your business that can increase efficiency, revenue and customer experience. Why not contact us to discuss further?
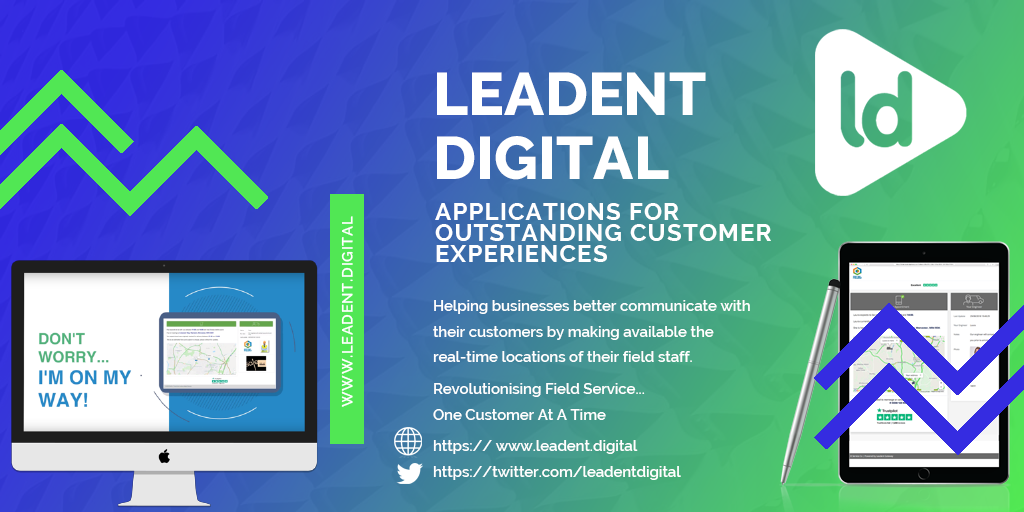